Micro-Optics
Ice Detection System
-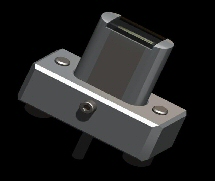
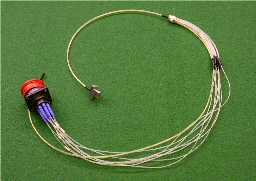
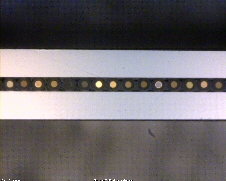
These two images represent the development of a fibre-optic probe, designed as part of an on-wing, leading edge ice detection system for large commercial aircraft. The sensor comprises a linear array of 36 multimode, polyimide coated optical fibres with a centrally located singlemode optical fibre sandwiched between two stainless steel plates, the sensing cassette. This cassette was then angle polished and mounted inside the sensor housing which was capped with a conformally polished sapphire window. Fibre protection is provided by a custom designed PTFE tube array with breakout box and specialised fibre termination into the military connector. Spare optical fibres are accommodated in a spare PFTE protection tube.
Dual Cavity Displacement Sensor
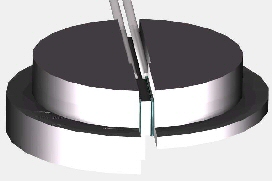

These two images show the construction of a low profile, dual fibre, displacement sensor. Based upon the differential measurement obtained from the formation of two optical cavities, each between the end face of the optical fibre and the object of interest, this component is capable of very precise distance measurement. However, the real innovation in this project was the turning and coupling of light through a 90 bend. Singlemode optical fibres are cleaved and angle polished at 45 degrees. The cleaved surfaces are then coated with a reflective metal and aligned with a horizontal singlemode fibre to enable coupling through 90 degrees. Each puck was manufactured in two halves which were subsequently bonded together following fibre endface polishing. The processes associated with the development of this component are a good indicator of the innovation and attention to detail required to address a significant measurement issue.
High Temperature Components
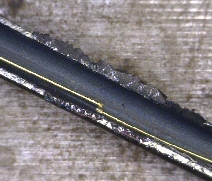


The three images above give examples of some of the high temperature components that have been developed and investigated. The first image shows a gold coated optical fibre that was pulled into a length of FIMT (fibre in metal tube) and tested at elevated temperature (~700oC). The second is a front diaphragm element of a high temperature acoustic sensor. The final image on the right shows the component under test at temperatures excedding ~650oC.