Ultra-miniature pressure sensors
Measurement Challenge
Provision of multiple point pressure measurements within a compliant material layer less than 2mm in thickness interposed between two rigid bodies under test. Modification of the structure was to be kept to a minimum with the deployment access to the sensing point locations being restricted to within the 2mm layer over a distance of several metres. Pressure sensing range: 0 to 2MPa. Minimum acceptable resolution: 2kPa.
Solution
Construction of a pressure sensor on the tip of a standard telecoms 125µm diameter silica optical fibre. The optical fibre having an overall diameter of 250µm, including primary buffer protective coating, was capable of being flexibly routed between the two rigid components without any modification of the system under test. An interferometric Fabry-Perot cavity was formed on the end of the optical fibre through using a hollow glass microspheres to form the cavity. Changes in pressure cause changes in the diameter of the microsphere which in turn result in pressure related changes in the optical path length of the Fabry-Perot cavity. These changes are then measured by monitoring the corresponding changes in the optical interference pattern produced by the optical cavity. The optical performance of the cavity was optimised by adjusting the optical reflectivity of the microsphere through the use of a gold coating.
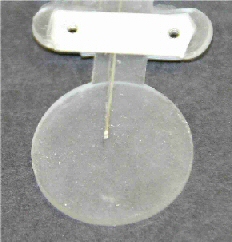
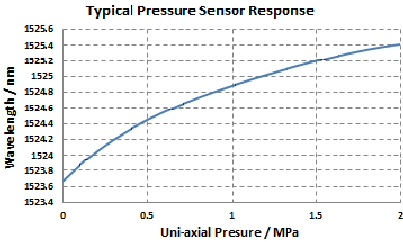
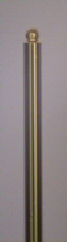
The first image shows a sensor encapsulated in a thin (2mm) silicone layer, the second indicates the improvement in Fabry-Perot response that can be obtained by coating the transducer and the third is an image of the bare sensing element.
This fibre-based pressure sensing configuration has a number of advantages over conventional technologies:
- The sensing element is extremely small. In some cases the limiting dimension being the optical fibre itself
- The pressure range and resolution can be tuned by selecting suitable microsphere properties, sphere diameter and wall thickness.
- Due to its extremely small thermal mass, transient pressure and temperature sensing are possible.
- Can be easily designed to measure strain and temperature.
If you wish to find out more about this application of optical fibre sensing please contact Dr. Tim Litt.